At AboutMechanics, we're committed to delivering accurate, trustworthy information. Our expert-authored content is rigorously fact-checked and sourced from credible authorities. Discover how we uphold the highest standards in providing you with reliable knowledge.
What is Tack Welding?
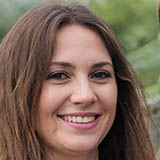
Tack welding is a technique where people create short welds at isolated points to hold two or more pieces of metal together during the fabrication process. This method creates a temporary joint to hold the metal in position, not a permanent one, and the welder will need to go back over the project to finish the welding. This process is an important part of metal fabrication with many kinds of items, and it must be performed properly for safety and the integrity of the finished project.
A simple example of tack welding can be seen when a welder wants a perpendicular joint between two pieces of metal, creating a T-shaped object. If the welder simply clamps the metal and starts welding, there is a risk of warping and deforming the joint during the welding process, pulling the metal out of alignment. The finished joint is firmly welded and cannot be adjusted if the welder makes a mistake. Instead, the welder starts with tack welding, creating a few short welding points around the joint to fix it in position before going over it to finish the job.
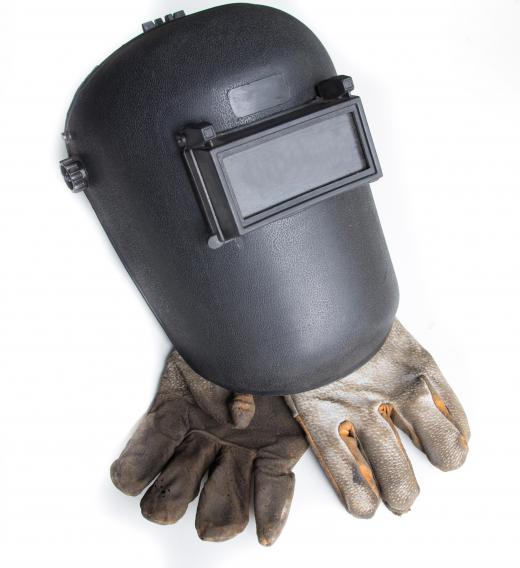
Welders can temporarily fix metal in place with tack welding while working on projects to make sure the metal is in the right position before creating a final weld. The tack welding is more flexible, allowing for small adjustments to the position of the metal. If there is a mistake, the welder can easily separate the pieces and start over, or swap in a new piece if a piece is not the right one for the job.
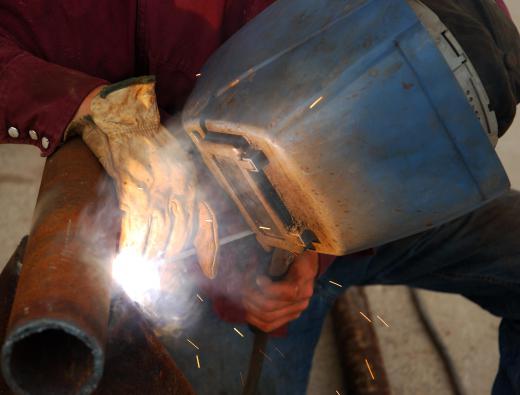
These temporary welds are not very strong. While they will hold the metal, they cannot bear stress or strain. Workers need to be aware that pieces only have tack welds in place and should exercise caution around the project. It's important to avoid standing under the metal, pulling on it, or creating hazards by stacking objects on top of it. As workers finish final welds, the project will be stronger and more capable of bearing stress.
In tack welding, welders must be careful about introducing defects to the project. The tack welds need to be clean, and welders should check for signs of metal fatigue or strain like cracks, fissures, discolorations, and so forth. If materials spill during the welding process they need to be carefully removed, as deposits of material like flux can create a hazard by weakening the metal or making it harder to create the final weld.
AS FEATURED ON:
AS FEATURED ON:


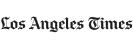

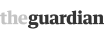
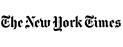
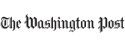


Discussion Comments
@RocketLanch8- I also used a tack welder at my job, but I was also responsible for making a more permanent weld later on. The manufacturing process involved tack welding a casing together, except for the top lid. The casing would be sent over to a station where someone installed a motor and then sent it back to me. I'd make the permanent welds and then attach the lid. If the motor didn't fit quite right, I could always break the tack welds and start over.
I had a job at an electric motor factory years ago, and one of my duties was to tack weld pieces of a frame together and send it down the line to the actual welding department. I had a small spot welder, and I would assemble the frame while it was on a pallet. I'd put two small welds at each corner and then move the pallet to the welding station. At that point, the weld was so weak that I could have broken the frame apart with my hands.
Post your comments