At WiseGEEK, we're committed to delivering accurate, trustworthy information. Our expert-authored content is rigorously fact-checked and sourced from credible authorities. Discover how we uphold the highest standards in providing you with reliable knowledge.
What is Slip Casting?
Slip casting is a term used to describe a technique that is used to mass-produce identical pottery or ceramic pieces. This technique is used either when the piece would be too difficult to produce on a potter's wheel, or when a cheap and quick means of mass production is desired. The technique involves the use of a liquid clay mixture, plaster molds, and a kiln. Many objects from simple plates and pots to complex decorative items and ceramic dolls can be produced by slip casting.
The process of slip casting begins with the selection of molds. Mold selection is first because there are many different types of slip available, and each type is made for different size pieces and different firing temperatures. Once the mold is selected, proper slip selection follows. Slip is liquid clay, but it is not made by simply adding water to solid clay. There are chemicals added to reduce the amount of water needed and to reduce the plasticity of the clay.
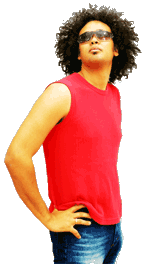
Once the desired mold and appropriate slip have been selected, the slip is mixed in a tool called a blunger, and is then poured into the plaster molds. A plaster mold is composed of a block of plaster that has the desired design carved inside and is then cut in half. There is also a pour hole added – usually at the bottom of the mold – that allows excess slip to be removed. The mold usually is held together by large bands or straps.
After the slip has been poured into the mold all the way to the top of the pour hole, the plaster will begin to pull moisture from the slip, causing the slip to form a hardened shell on the inside of the mold. When this shell is 1/8- to 1/4-inch (about 3.28 to 6.35 mm) thick, the excess slip is poured out for reuse and the mold is turned over to allow any leftover slip to drip out into a bowl or container. Certain items such as plates, however, can be poured solid. The mold and the hardened shell it contains are allowed to sit until the hardened shell is dry enough to remove from the mold without damage. This process usually takes anywhere from 15 minutes to an hour, depending on the size and thickness of the piece, as well as the climate and type of slip used.
When enough time has elapsed, excess clay is cut off of the piece at the area where the pour hole joins the molded piece; the first half of the mold then is gently removed. Once again, the piece is allowed to sit for a few minutes before it is gently removed from the other half of the mold. Upon removal of the piece from the mold, the product is known as greenware. It is very delicate and has seams that must carefully be removed with special tools that cut and scrape the dried clay off of what will be the finished piece. This typically should not be done for 24 hours after removing the greenware from the mold to allow sufficient drying time.
After the greenware has been cleaned, the slip casting process is almost complete. Decoration and firing are the only steps that remain. Before firing in a kiln, certain types of paints called under-glaze can be used on greenware to give it vibrant and detailed color prior to glazing and a second firing. Once a piece has been fired, it is referred to as bisque and can then be glazed and fired a second time to give it either a clear, shiny sealant or specialized colors and textures for a unique look. After cleaning, the process is almost the same for a slip cast piece as for a piece that has been thrown on a pottery wheel or has been sculpted.
Because slip is relatively inexpensive and mass-production simple, the value of a piece created through ceramic slip casting is less than that of a hand-thrown piece. There are some ceramic artists that try to pass off pieces made from commercial molds as unique or hand-thrown, but anyone with knowledge of the process can know what to look for. Any seaming on the underside or any part of the piece that was not properly removed is a dead giveaway that a piece was poured and likely mass-produced. If all the pieces in a set are identical, it is very unlikely that the pieces were hand-thrown on a wheel. Sometimes ceramic artists will hand throw or sculpt an original piece and then create a mold of the piece for reproduction purposes; in this case, the value may be slightly higher than pieces produced through use of commercial molds.
AS FEATURED ON:
AS FEATURED ON:


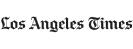

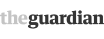
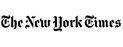
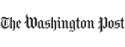


Discussion Comments
Your point is so true Heavanet. I also think that handmade ceramic products are usually heavier and better made than those made by clay slip casting.
I understand the need for mass production to make a lot of ceramic products quickly and effectively, but it is a shame that slip casting equipment has replaced many artistic clay sculptors. When clay was thrown on a potter's wheel and molded into place, the end result was unique and high-quality. There are still companies that mold ceramic products this way, and I enjoy looking for these pieces for their beauty, durability, and artistic quality.
Post your comments