At AboutMechanics, we're committed to delivering accurate, trustworthy information. Our expert-authored content is rigorously fact-checked and sourced from credible authorities. Discover how we uphold the highest standards in providing you with reliable knowledge.
What Is Involved in Pouring Silicone?
The first step in pouring silicone is gathering the necessary materials. A master piece of some sort will be needed to create the mold; this master piece will give the shape to the mold, allowing the user to create duplicates of that piece. The master should be made of plastic, since the silicone will not bond to plastic and will therefore create the mold without tearing, splitting, or otherwise becoming damaged. A few different types of knives will be necessary for this process, as will a structure that can contain the mold, the silicone mixture itself, and a releasing agent.
Pouring silicone starts with creating a base and wall structure that can contain the silicone in its liquid form. This can be done with a variety of materials, and kits are available for purchase to make the process much easier, depending on the size of your project. Once the structure is in place, the piece to be molded is set inside; it must be raised off the base a bit, usually with small braces, so the silicone can be poured on all sides of the piece. The master piece must be properly in place before the user starts pouring silicone, or the mold will be imperfect. The piece must also be inspected carefully for burrs or imperfections.
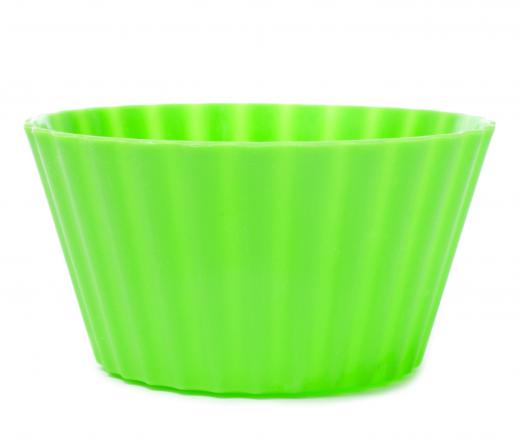
The silicone material usually comes in two bottles. The components of the silicone are mixed together by a 1:1 ratio. The master should be sprayed with wax to facilitate removal of the silicone once the process has been completed. Once the mixture of silicone is ready, it can be poured into the mold container around the master piece. The silicone solution must cover all parts of the master, and it must be thick on all sides to prevent a weak final mold. Pouring silicone slowly will prevent air bubble pockets from forming in the final mold.
After the silicone has been poured, it must cure for 24 hours. It will harden, but it will still be pliable. The mold will be removed from the container and cut in half; once the blade reaches the master piece in the center, the two pieces of silicone can be pulled apart gently. While silicone is pliable, it can still tear, so the process of pulling the two pieces apart must be done slowly and carefully. The two halves of the silicone mold are then sprayed with a releasing agent to prevent the plastic to be molded from sticking to the silicone.
AS FEATURED ON:
AS FEATURED ON:


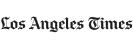

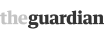
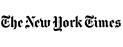
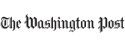


Discussion Comments
I use silicone mold making compounds for small craft projects like jewelry and doll faces.
One thing to remember when pouring silicone is to think about the size of your project. Depending on what type of silicone compound mixture you use, you may not have a lot of time before the mixture starts to get hard.
This is fine if you are working with small pieces, but if you have a large project, you need to use something that gives you more time.
I have also learned not to rush the amount of time you let your mold sit and get completely hard. This was one of those things that was learned the hard way.
The temperature and humidity can make a big difference, so I always allow enough time for the mixture to be set all the way through.
@SarahSon - I always thought silicone mold making looked difficult and time consuming. I went to a class on how to make silicone molds and realized how fun it could be.
You are right when you say how creative you can be when it comes to making your own molds. Once you get an original done, you can use that over and over again.
If you are going to making silicone molds for candy or mints, make sure you use a product that is food grade. This means the material you use in your mold is safe for making products you can eat.
If anybody makes their own soap, you know how much easier a silicone mold is to work with than plastic. A silicone mold is flexible and your finished product releases so much easier.
Another advantage to silicone is if you have a lot of detail in your mold, you know it will look great every time. They are also heat resistant which makes it nice when you are working with certain types of material.
Since I started making my own silicone rubber molds for my soaps, I have really increased my business. By making my own molds, I can easily customize orders for someone and have unique designs that you don't find everywhere else.
Post your comments