At AllTheScience, we're committed to delivering accurate, trustworthy information. Our expert-authored content is rigorously fact-checked and sourced from credible authorities. Discover how we uphold the highest standards in providing you with reliable knowledge.
What Is Hydroforming?
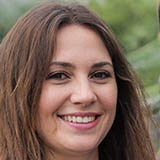
Hydroforming, a technique used to produce metal parts, uses a high-pressure liquid to force a thin sheet or tube into a mold. The result can be a seamless part that is extremely lightweight, strong and durable. Manufacturers can produce custom hydroformed parts by request and can make generic parts for mass sale and distribution. The costs for custom pieces can depend on the order's size and complexity. For the fabrication of specialty components, costs can be very high, because technicians might need to spend some time on the development of technical specifications and plans before creating the mold.
One hydroforming technique utilizes a bladder filled with fluid. A technician places a flat sheet of metal over a mold and closes the mold, with the bladder applying pressure on one side. The technician increases the pressure, and the bladder forces the metal into the mold. When the technician opens the two halves, the fully formed piece can be removed. High levels of detail are possible with this method, and the metal can be very thin for lightweight production techniques.
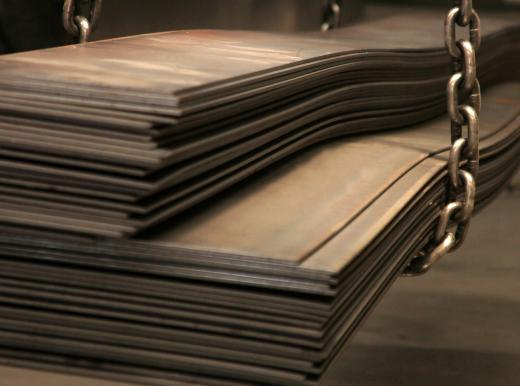
Another option is tube forming. In this variation, the technician closes a tube inside a mold with a shape cut out somewhere along the length of the tube and uses blocks to hold the mold in place. Next, the technician pumps very high pressure into the metal tube. The tube expands outward to accommodate the pressure and conforms to the shape of the mold. The technician can drain the tube and remove it from the mold, revealing a complete part.
The costs of hydroforming can increase with large, complex molds. Technicians might need to experiment with the mold and the fluid to get the right level of pressure, and this might require making several trial pieces before moving on to final production. For some components, the seamlessness and durability are worth the cost of hydroforming. Companies in the industry also constantly have new techniques in development to lower costs and increase reliability.
If a company needs hydroforming, it can be worth soliciting bids from several manufacturers. This will provide valuable information about the range of costs and the capacity of different manufacturers. Some specialize in forming components for particular industries and might be able to offer competitive rates on products in those industries. For a company that wants to produce its own components, it also is possible to purchase equipment for hydroforming. Used and rental equipment might be available for companies that are concerned about costs.
AS FEATURED ON:
AS FEATURED ON:


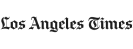

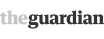
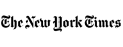
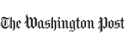


Discuss this Article
Post your comments